Vehicle Thickness
-
- Member
- Posts: 35
- Joined: Thu Feb 21, 2019 3:24 pm
- Division: B
- State: MA
- Has thanked: 0
- Been thanked: 0
Re: Vehicle Thickness
For those of you with 10-20 cm thick vehicles, isn't that too thin to implement a wingnut brake that can rewind to 12 meters?
Re: Vehicle Thickness
Quite easy unless your using like 2 inch diameter wheels. Use 4 inch wheels and you could probably make it 8cm! Really gets more the the question of losing accuracy left/right at some point. I saw quite a few cans smucked last week.invisiblebanana wrote:For those of you with 10-20 cm thick vehicles, isn't that too thin to implement a wingnut brake that can rewind to 12 meters?
-
- Exalted Member
- Posts: 774
- Joined: Sun Nov 19, 2017 9:09 am
- Division: C
- State: RI
- Has thanked: 211 times
- Been thanked: 56 times
Re: Vehicle Thickness
Wdym losing accuracy left/right?builder83 wrote: Quite easy unless your using like 2 inch diameter wheels. Use 4 inch wheels and you could probably make it 8cm! Really gets more the the question of losing accuracy left/right at some point. I saw quite a few cans smucked last week.
Re: Vehicle Thickness
Just meant that the narrower the buggy becomes the more an adjustment compounds its steering. You could build a battery motorcycle 3 cm wide but but good luck steering it! I didnt try a buggy under 10 cm though so I will differ to those who have tried. Anybody try anything ridiculously thin with any consistant accuracy?MadCow2357 wrote:Wdym losing accuracy left/right?builder83 wrote: Quite easy unless your using like 2 inch diameter wheels. Use 4 inch wheels and you could probably make it 8cm! Really gets more the the question of losing accuracy left/right at some point. I saw quite a few cans smucked last week.
-
- Member
- Posts: 63
- Joined: Sun Jan 27, 2019 5:37 pm
- Division: C
- State: PA
- Has thanked: 5 times
- Been thanked: 0
Re: Vehicle Thickness
We have our lead screw running from the back of the vehicle to the front. The motor drives the screw at the rear, and a pair of bevel gears join the lead screw to the front axle to drive the front wheels.invisiblebanana wrote:For those of you with 10-20 cm thick vehicles, isn't that too thin to implement a wingnut brake that can rewind to 12 meters?
2019 - 2020 Events
~ Boomilever
~ Detector Building
~ Gravity Vehicle
~ Machines
~ Ping-Pong Parachute
~ Boomilever
~ Detector Building
~ Gravity Vehicle
~ Machines
~ Ping-Pong Parachute
-
- Member
- Posts: 276
- Joined: Tue Mar 24, 2015 8:21 am
- Division: B
- State: NY
- Pronouns: He/Him/His
- Has thanked: 6 times
- Been thanked: 3 times
Re: Vehicle Thickness
Tendan wrote:We have our lead screw running from the back of the vehicle to the front. The motor drives the screw at the rear, and a pair of bevel gears join the lead screw to the front axle to drive the front wheels.invisiblebanana wrote:For those of you with 10-20 cm thick vehicles, isn't that too thin to implement a wingnut brake that can rewind to 12 meters?

-
- Exalted Member
- Posts: 774
- Joined: Sun Nov 19, 2017 9:09 am
- Division: C
- State: RI
- Has thanked: 211 times
- Been thanked: 56 times
Re: Vehicle Thickness
Oh c'mon! And I was really hoping I was the only one who thought of this...SPP SciO wrote:Tendan wrote:We have our lead screw running from the back of the vehicle to the front. The motor drives the screw at the rear, and a pair of bevel gears join the lead screw to the front axle to drive the front wheels.invisiblebanana wrote:For those of you with 10-20 cm thick vehicles, isn't that too thin to implement a wingnut brake that can rewind to 12 meters?Something similar to this? My students showed me this, but it looks costly to invest in at this point in the season - that's a lot of parts that need to be perfectly compatible. They had originally tried building a narrower car early in the season, but ran into the same problem with running out of thread space for the wingnut on the longer runs. Part of the problem also was using a lead screw rather than a typical hardware store threaded rod; the different thread spacing had a noticeable effect.
Any reason why the two axles are connected?
-
- Member
- Posts: 276
- Joined: Tue Mar 24, 2015 8:21 am
- Division: B
- State: NY
- Pronouns: He/Him/His
- Has thanked: 6 times
- Been thanked: 3 times
Re: Vehicle Thickness
That's not a diagram of an actual battery buggy, just a "design idea" picture you see when you check out bevel gears at servocity, so I'm not sure what function they were going for. I'd be interested to know how using the bevel gears to move the wingnut parallel to the overall direction of movement would play out. Those servocity gears are designed to fit the 1/4" D shafting, which would need to be modified to fit a typical 1/4" threaded rod. It would be able to trip a switch, but can it effectively lock up the wheels at the same time? Also, is it correct to assume that the gear ratio will change the linear distance traveled by the wingnut? That's interesting for accuracy purposes - maybe if the distance is "stretched out" to 2x as long as usual, it's easier to set the wingnut with a ruler, rather than counting rotations. I hope you experiment and keep us postedMadCow2357 wrote: Oh c'mon! And I was really hoping I was the only one who thought of this...
Any reason why the two axles are connected?
-
- Member
- Posts: 35
- Joined: Thu Feb 21, 2019 3:24 pm
- Division: B
- State: MA
- Has thanked: 0
- Been thanked: 0
Re: Vehicle Thickness
You could always use a 1:1 gear ratio for the bevel gear if you're concerned with accuracy.SPP SciO wrote:That's not a diagram of an actual battery buggy, just a "design idea" picture you see when you check out bevel gears at servocity, so I'm not sure what function they were going for. I'd be interested to know how using the bevel gears to move the wingnut parallel to the overall direction of movement would play out. Those servocity gears are designed to fit the 1/4" D shafting, which would need to be modified to fit a typical 1/4" threaded rod. It would be able to trip a switch, but can it effectively lock up the wheels at the same time? Also, is it correct to assume that the gear ratio will change the linear distance traveled by the wingnut? That's interesting for accuracy purposes - maybe if the distance is "stretched out" to 2x as long as usual, it's easier to set the wingnut with a ruler, rather than counting rotations. I hope you experiment and keep us postedMadCow2357 wrote: Oh c'mon! And I was really hoping I was the only one who thought of this...
Any reason why the two axles are connected?
My design also uses the ServoCity aluminum channel, and the wingnut brake locks up the wheels decently. Sometimes it pushes the wingnut into the ball bearing hub a little bit so the wheels don't really turn in any direction, but a little bit of force fixes it. The gears also fit my 1/4 in threaded rod perfectly, but idk about if it'll fit everyone's.
Madcow: Are you also using the ServoCity channel and bevel gears? And I guess the bevel gears are connected to ensure that the vehicle will completely stop moving once the wingnut locks up, but it seems a little unnecessary.
I think we'll see many designs like that at nats
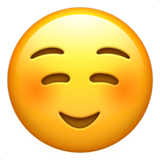
-
- Member
- Posts: 63
- Joined: Sun Jan 27, 2019 5:37 pm
- Division: C
- State: PA
- Has thanked: 5 times
- Been thanked: 0
Re: Vehicle Thickness
Our setup is a bit simpler than that, but it's the same idea. The main differences are:SPP SciO wrote:Tendan wrote: We have our lead screw running from the back of the vehicle to the front. The motor drives the screw at the rear, and a pair of bevel gears join the lead screw to the front axle to drive the front wheels.Something similar to this? My students showed me this, but it looks costly to invest in at this point in the season - that's a lot of parts that need to be perfectly compatible. They had originally tried building a narrower car early in the season, but ran into the same problem with running out of thread space for the wingnut on the longer runs. Part of the problem also was using a lead screw rather than a typical hardware store threaded rod; the different thread spacing had a noticeable effect.
1. Our setup has the motor driving one pair of wheels, instead of the two pairs that the example would be powering.
2. We are using a 1:1 gear ratio.
3. Our support structure is made up of one solid 3D printed piece.
4. A lead screw runs between the motor and gears. It would sort of be where the long axle is in the picture.
The gears we found are on servocity for $30 for 2. If you have spare bearings and access to a 3D printer, you shouldn't have to buy much else to be able to replicate the idea in the photo without having to buy all of the structural parts and additional bearings. That being said, if your team doesn't have a member proficient in 3D modeling, it might be better to buy the support structure too.
2019 - 2020 Events
~ Boomilever
~ Detector Building
~ Gravity Vehicle
~ Machines
~ Ping-Pong Parachute
~ Boomilever
~ Detector Building
~ Gravity Vehicle
~ Machines
~ Ping-Pong Parachute