Page 10 of 15
Re: Boomilever for 2013
Posted: July 22nd, 2012, 2:44 pm
by SLM
iwonder wrote:Even if you needed bracing for multiple tubes, would'nt it still be more efficient to build the member out of tubes becuase they offer almost the same buckling strength compared to a solid member, and weight a lot less?(they would offer the same strength, right?)
Instead of using a tube of diameter D, if we use two tubes of diameter D/2 each, we have reduce the governing moment of inertia of the member by a factor of 4. That is, if the larger tube has a moment of inertia of I, then the properly braced double tube section would have a moment of inertia (in the weaker direction) of approximately I/4.
Although a tubular section is more economical than a rectangular one with regard to buckling, but you will run into problems if you decide to brace the tube. More specifically, compared with the rectangular section, a tube has a very thin wall. It would not be wise to apply a point load to the wall in the weaker direction (unless the tube is braced adequately at that point). Any bracing that is directly attached to the thin wall of a tubular member will eventually exert a force on the wall, most likely, causing a failure.
Re: Boomilever for 2013
Posted: July 22nd, 2012, 2:50 pm
by SLM
iwonder wrote:... Speaking of the SAN, does anyone know why it's giving me displacements in members but I'm not seeing any stresses/forces?
I would be interested in knowing why you are not getting any values for the stresses/forces. What values are you using for modeling your structure (geometry, section sizes, modulus of elasticity, support types, and loads)?
Re: Boomilever for 2013
Posted: July 22nd, 2012, 3:09 pm
by iwonder
If I remember correctly...
Geometry was the same as the truss I posted above(same nodes/members), 40cm long and 6cm wide.
The two main members were tubes, always 1/32"(.8mm) thick, I tried a lot of different options as to major diameter(5/16" up to 1/2"), the cross members were 1/8"by1/32" rectangles.
I used 528,827 kPa as a modulus of elasticity.
Both nodes on one end were grounded, the other two had a load of 500N each(I know this is a little extreme... but I was just trying it out).
Re: Boomilever for 2013
Posted: July 22nd, 2012, 3:17 pm
by SLM
T-B wrote:...I still need to think through the dilemma about how you would attach the tension chords to the tubes. Not much gluing surface.
If a single tube is being used, what about a simple horizontal frame attached to the center of the tube for accommodating the load block, like this:

Re: Boomilever for 2013
Posted: July 22nd, 2012, 3:35 pm
by iwonder
Those drawings are just awesome...
Wouldn't that still put a point force on the tube?(Well 2 forces...) Then again, if the members are long enough, it wouldn't make much difference, would it?
Re: Boomilever for 2013
Posted: July 22nd, 2012, 3:54 pm
by jander14indoor
iwonder wrote:<SNIP>Edit: Oh, and anyone looking to buy arrow shafts, if you don't have a local shop, the big name sporting goods stores sometime sell arrows for bow fishing(specifically, arrow blanks) that aren't carbon fiber and in the $50-$90 price range.
Have trouble believing there isn't an archery shop or general purpose sporting goods store with archery equipment that far from almost anyone. And that's a crazy amount to spend, heck, if you sweet talk a shop they'll probably give you cast offs for free. Just remember to thank them.
Alternatively, copper plumbing comes in a variety of sizes, easier to bend, but 1/4 or 3/8 copper tube will be in the range.
On-line, try a phone call, if you can get to a real person, not an order taker, sweet talk about what you are doing might get something cheap.
Or, you could order Stainless steel rod or tubing from Small Parts or McMaster Carr for less than that amount. Get the good surface finish stuff.
SLM wrote:T-B wrote:...I still need to think through the dilemma about how you would attach the tension chords to the tubes. Not much gluing surface.
If a single tube is being used, what about a simple horizontal frame attached to the center of the tube for accommodating the load block, like this:
<SNIP a great drawing>
You probably want something with a smoother transition, abrupt changes like that are problematic at best. The problem isn't the length of the section glued inside the tube, but the abrupt change from sticks to tube. However deep your sticks are, the stress risers are where the sticks enter the tube. Go back and look at that monocoque elevated bridge posted previously for inspiration. Smooth transition from one section to the other.
Jeff Anderson
Livonia, MI
Re: Boomilever for 2013
Posted: July 22nd, 2012, 5:48 pm
by SLM
iwonder wrote:If I remember correctly...
Geometry was the same as the truss I posted above(same nodes/members), 40cm long and 6cm wide.
If I understand you correctly, you want to analyze the following structure.
SAN can only analyze structures whose members and loads are on the same plane. Here, however, although the structure lies on the xy plane, the loads are on a different (vertical) plane. For this, you need a more advanced structural analysis software.
Regardless, I am not sure why you are analyzing the compression members only. If you were to analyze the entire boom, since there is a vertical plane of symmetry (the vertical plane that goes between the two compression members), then you can use SAN to analyze one half of the structure (a compression member, the tension member attached to it, the supports at the ends of the two members, and the 500 N load).
Re: Boomilever for 2013
Posted: July 22nd, 2012, 5:54 pm
by iwonder
You're Have a good point about analyzing the whole structure(I plan on doing that, but I use FEA in autodesk inventor for those kinda of analysis), and I had the 500N load 'pointed' towards the grounded end, so it was axial to the tubes. I'm still not quite sure why one couldn't test the compressive member seperate however... If I remember it had something to do with strain in the members coming from the structure as a whole, but I just can't wrap my head around it... Sorry
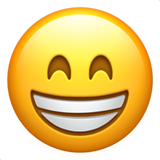
Re: Boomilever for 2013
Posted: July 22nd, 2012, 7:34 pm
by SLM
iwonder wrote:You're Have a good point about analyzing the whole structure(I plan on doing that, but I use FEA in autodesk inventor for those kinda of analysis), and I had the 500N load 'pointed' towards the grounded end, so it was axial to the tubes. I'm still not quite sure why one couldn't test the compressive member seperate however... If I remember it had something to do with strain in the members coming from the structure as a whole, but I just can't wrap my head around it... Sorry
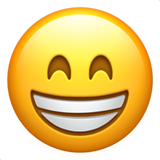
If the loads are applied axially in the plane of the frame, then the structure can be analyzed using SAN. Here is the analysis results based on my interpretation of your input data:
http://dl.dropbox.com/u/54640248/SAN-1.pdf
The missing tension members contribute to the stiffness of the structure, which in turn effects the joint displacement and the member forces. In general, unless you can accurately model the stiffness of the substructure (the boom without the tension members), the outcome of its analysis would not be the same as that of the entire structure.
EDIT: By the way, FEA is a good technique for examining the stress concentration issue that has been raised by jander14indoor.
Re: Boomilever for 2013
Posted: July 23rd, 2012, 5:46 am
by SLM
jander14indoor wrote:
SLM wrote:
If a single tube is being used, what about a simple horizontal frame attached to the center of the tube for accommodating the load block...
You probably want something with a smoother transition, abrupt changes like that are problematic at best. The problem isn't the length of the section glued inside the tube, but the abrupt change from sticks to tube.
The idea (illustrated below) is to attach a horizontal frame to the end of the tube that could transfer compression force in the direction of the wood grains without exerting any significant force on the tube in its weaker direction.
Here are two ideas that may help addressing potential stress concentration and effective stress transfer to the tube.
Let's visualize the unfolded tube at the load end:
To reduce potential stress concentration at the point of contact between the tube and the stick, and to save material, we can cut the end of the tube like shown below.
Further, to make sure the thin tube (where it is connected to the stick) has adequate compressive strength to effectively withstand the stress, we can stiffen it by increasing its thickness as shown below.
Of course, the size of the stick for transferring the compression force to the tube, the size of the cut at the end of the tube, and the thickness and length of the stiffeners need to be determined experimentally.