Boomilever B/C
-
- Admin Emeritus
- Posts: 1115
- Joined: May 10th, 2011, 8:25 pm
- Division: Grad
- State: TX
- Has thanked: 0
- Been thanked: 1 time
Re: Boomilever B/C
^Thanks bear...
Balsaman, any tips for the construction of the distal end? I've looked through aia's guide, but every time I go to do the connection(This'll be my 4th boom) I always end up having to slide the pieces around while clamped(gorilla glue) until it looks right. Are there any little tricks for lining things up without relying on looks? I'm mainly trying to get the loading block center and the compression member's center in line and make sure it all sits square to the wall with a little preload angle, but that's pretty difficult to eyeball.
Balsaman, any tips for the construction of the distal end? I've looked through aia's guide, but every time I go to do the connection(This'll be my 4th boom) I always end up having to slide the pieces around while clamped(gorilla glue) until it looks right. Are there any little tricks for lining things up without relying on looks? I'm mainly trying to get the loading block center and the compression member's center in line and make sure it all sits square to the wall with a little preload angle, but that's pretty difficult to eyeball.
'If you're the smartest person in the room, you're in the wrong room' - Unknown
-
- Coach
- Posts: 1318
- Joined: November 13th, 2008, 3:01 am
- Division: C
- State: CO
- Has thanked: 0
- Been thanked: 3 times
Re: Boomilever B/C
Sure; the short answer is jigging- you can best attack this problem by building a jig or jigs to hold things in proper alignment. Trying to do this by eyeballing it is going to lead to enough variability boom-to-boom to cause you MAJOR problems.iwonder wrote:^Thanks bear...
Balsaman, any tips for the construction of the distal end? I've looked through aia's guide, but every time I go to do the connection(This'll be my 4th boom) I always end up having to slide the pieces around while clamped(gorilla glue) until it looks right. Are there any little tricks for lining things up without relying on looks? I'm mainly trying to get the loading block center and the compression member's center in line and make sure it all sits square to the wall with a little preload angle, but that's pretty difficult to eyeball.
This question/problem goes right to my point #5, above, and you are right-on to recognize the importance of, let’s call it “shape control.” It applies to booms, and towers, and bridges – any structure built up from pieces/members. It is one thing to ‘design up” a structure, where everything is aligned- parallel/perpendicular/symmetrical, and you know the loads on the various members/joints, and you have the right cross sections & densities to carry those loads. It can be quite a challenge to actually build “to the design.” As you understand, as things get “out of line”, when the structure is loaded, the forces the various members experience change from the “design” forces. If you have the density and size of a particular member “just right”- just sufficient for the force it will see at full load- and the shape/alignment of the structure is not “perfect’, then that piece, and other pieces will see more than the design force, and will fail prematurely. How much “mis-alignment” causes how much of a change in forces seen at load a) depends on which members, and b) gets pretty complex to calculate.
What you get into is an interplay between – tradeoffs between precision of shape and the level of safety factor needed – the truer the shape, the closer the forces (when the structure’s loaded) to the design forces, and the more equally distributed the forces are (for instance, between two tension members), and the lower the “other” forces- like twisting, bending- are. How precise you can get the “shape control’ depends mostly on how much time you’re willing/able to put into the problem. It is time well spent; it WILL pay off, in terms of how light you can get the structure. What REALLY pays off is getting “repeatability’ in structure shape/alignment – getting so that when you build a second, third, fourth, etc. one, it is the same shape. If you don’t do that- if the shape/alignments change, then any attempt to adjust strength (size & density) of members to get the weight down is is a complete waste of your time- you’re shooting in the dark- forces at load keep changing; you don’t know where or by how much…..
The way to get to shape control is good jigging – jigs hold pieces firmly and precisely in place/in alignment for glueing. Exactly how to design/build depends on what you’re trying to align, and the materials and tools you have access to. Basically, you want to envision/position pieces “in-place”, and figure out what you need to build to hold them where you want them. The strength of the jigging only needs to be enough to hold against any forces put on when doing the assembly. The precision of the jigging needs to be as good as you can get it- very precise measurement, and cutting, and then positioning.
Our “base jig” is two pieces of pressboard – shelving- 12” wide. The bottom piece is what the compression member lies on; it’s 24” long. The “wall” piece is about 18cm long. It is mounted vertically on/across the base piece. This is very carefully aligned- square across the bottom piece, and at a 90 degree angle to it. One edge is so that the base part provides 42.6cm (the 40cm minimum from the wall distance + 1mm, + 2.5cm for the outer half of the load block. Get and use a really precise square; we use a draftsman’s 30-60-90 that’s about 16” long. We use right triangles carefully cut from the same pressboard, put on the back side of the wall piece to align/brace it. All lines are marked with a very sharp pencil, cuts done on a good table saw. The (horizontal) line of the bolt holes is very carefully marked – measuring on both sides from the bottom edge of the wall piece. (vertical) Centerline is carefully marked. A cross line on the bolt line is marked 10cm to either side of center- a center and the two side bolt holes are drilled. The height of the bolt centerline above the bottom of the wall piece is 14.90cm plus the thickness of a sheet of 3/32nds plexiglass. That’s so we can use plexi surfaces on the jig- wall and base. The plexi allows very precise line marking. When you have the wall piece drilled (using a drill press so the holes are perpendicular to the wall), cut a piece of plexi to the same size as the wall piece. Put the plexi up against the wall piece, with the bottom edges down on a hard, flat surface; holding them vertically, tape the edges, so the plexi is firmly positioned on the pressboard. Carefully aligning on the drill press, with the plexi side down, running the drill down through the holes in the pressboard, and drill the bolt holes in the plexi. Very carefully, scribe (as in gently scratch) a vertical centerline- perpendicular to the bottom edge, runs through the center off the center bolt hole. Now cut a piece of plexi that fits the base plate. Be very careful to get it cut square- particularly the edge that goes up against the wall. Very carefully scribe a centerline along its length. A trick to make thee scribe lines easily seen is to mark the line with a magic marker- a nice wide line- like 1/8th’ wide- then scribe down the middle of that colored line. Using tape, position the wall plexi piece, and the base plexi piece. You want the centerlines to line up very precisely. Then by careful measuring/scribing marks parallel to the centerline, you can place little holding blocks that will align the compression member exactly along the centerline.
Depending on how you’re doing your distal joint(s), if the ends of the tension pieces extend below the plane of the top of the base plate, you’ll want to mark, and then drill/cut/dremel clearance space for them. Definitely recommend doing this, because one of the keys to getting symmetrically aligned tension members is to be able to have them under a bit of tension when you glue the distal ends. If you initially make them long enough to extend a few centimeters below the bottom side of the base plate, and have holes through the base plate that clear them, and provide room enough to avoid glueing the boom to the jig, you can attach a puller to the ends under the bottom side. By making a yoke with a carefully centered “pull hole”, you can put a balanced pull on both. You want enough pull to make sure both are…..fully straightened out. You may want, and this is something you’ll have to work out, a shim at the distal end to lift the end up a bit. Under full load, the tension members will stretch a bit. If you align them so that before loading, the compression member is exactly perpendicular to the wall, at full load, the distal end will droop/drop down by some amount. How much that stretch will be depends on the wood you use for tension members. A reasonable starting place is on the order of 1/32nd shimming under the distal end, then figure out the right amount from testing.
That gets us to the last consideration – glue. Gorilla Glue has some good things going for it; it provides plenty of working time- you can easily move things around to get them carefully aligned; it is strong in shear- when in a thin layer. However, because of the need for a thin layer, and because it foams, if the pieces being glued are not under significant clamping pressure, the foaming will push the pieces apart, and result in a weak joint. Getting sufficient clamping pressure on the distal joints, and keeping it in-place for an hour or so, depending on exactly how you’re doing them, can be, as you’ve discovered, a real pain….. Even the jigging described above doesn’t provide an easy solution to this problem. Because of this, we went from Gorilla to slow CA- using the pull-yoke approach, and two people- using finger pressure- all you have to do is hold in-place for 30-45 seconds. If you run into issues with the brittleness of CA, there is an option – “rubberized”/flexible CA- has a little bit of flexibility, shear strength is about 1/3 greater than regular CA. it comes in both clear and black.
So, hope this helps.
Len Joeris
Fort Collins, CO
Fort Collins, CO
-
- Member
- Posts: 131
- Joined: February 5th, 2011, 1:33 pm
- Division: C
- State: CA
- Has thanked: 0
- Been thanked: 0
Re: Boomilever B/C
Tried base with 3 layers of 1/16" balsa, approx. 8lb/ft^3
Didn't use washer, about .5mm space between bolt and tension member.
Front and back, grain horizontal. middle, grain vertical.
Put a bit of super glue over surface, since it felt soft.
At 3.8kg, base snapped in half vertically.
I didn't take care to screw it on securely, I thnk I made it too loose...or just balsa was too compressable and weak.
The distal end support braces got messed up a bit when the block fell through.
Other than that, no other damage. Would you normally try to fix this and test again?
I'll use bass for top layer next time..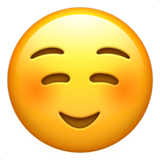
Didn't use washer, about .5mm space between bolt and tension member.
Front and back, grain horizontal. middle, grain vertical.
Put a bit of super glue over surface, since it felt soft.
At 3.8kg, base snapped in half vertically.
I didn't take care to screw it on securely, I thnk I made it too loose...or just balsa was too compressable and weak.
The distal end support braces got messed up a bit when the block fell through.
Other than that, no other damage. Would you normally try to fix this and test again?
I'll use bass for top layer next time..
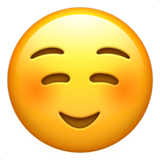
-
- Coach
- Posts: 1318
- Joined: November 13th, 2008, 3:01 am
- Division: C
- State: CO
- Has thanked: 0
- Been thanked: 3 times
Re: Boomilever B/C
A few thoughts back that may help-_HenryHscioly_ wrote:Tried base with 3 layers of 1/16" balsa, approx. 8lb/ft^3
Didn't use washer, about .5mm space between bolt and tension member.
Front and back, grain horizontal. middle, grain vertical.
Put a bit of super glue over surface, since it felt soft.
At 3.8kg, base snapped in half vertically.
I didn't take care to screw it on securely, I thnk I made it too loose...or just balsa was too compressable and weak.
The distal end support braces got messed up a bit when the block fell through.
Other than that, no other damage. Would you normally try to fix this and test again?
I'll use bass for top layer next time..
First, there is a very helpful tool/approach for the ….testing/development cycle (build/test/break/adjust-refine/re-test, etc.)- using some sort of a “safety tower”- a way to limit/adjust the distance the load block can fall. That way, when something fails, the load block only falls, say 1/8th….1/4”. Damage is – if adjusted right – limited to the initial failure; no…..secondary damage; you know exactly what the initial failure mode was- can easily repair/strengthen up that, and re-test to see what goes next, beef that up, etc- can run multiple tests in a day. Exactly how to set it up depends on your test rig. What you need to set up is a support point above the load block (that’ll hold 15+kg). Get a coupling nut, and put it on the threaded/upper end of the eyebolt that goes thru the load block. Put another eyebolt- with the eye up, into the coupling nut- run little chain, or cable up from that upper eye to your support point. If you use another eyebolt for the support point, and work out your dimensions, by rotating the eyebolts, you can adjust the distance the load block can move downward.
Second, for a number of reasons, you definitely want to tighten the bolt(s) in the tension member attachment pieces, and do it consistently.
Third, 8 lb/cu ft balsa is pretty darn light- soft/compressible when…..side-loaded- when the force is perpendicular to the grain. It will crush at a force WELL below what you’ll be putting on it at full (15kg) load- with 2 tension members, you’re looking at a force per tension member of at least 22kg. Replacing the layer away from the wall with bass will definitely improve the crush resistance. Now, and we’ll get back to this in a second, the crush strength of balsa parallel to the grain- ‘end grain’ loading is a lot higher….
Fourth, why did you choose to not run a washer? A washer allows the force you have to carry to be spread out over a significantly larger area- reduces the load in pounds per square inch a lot- bolt head bearing area vs washer bearing area…4-5 times as much.
Fifth, you’re on the right track with lamination to stiffen the base piece/plate, and with crossing the grain orientations – making a piece of plywood. But by only having it 3/16ths thick, you’re really limiting yourself, and the…..strength performance of the plate, in two important ways. Can’t tell from your description, but it sounds like the tension member(s) positioned to the side of (rather than at the top of the bolt(s)), and the pull under load is bending/bowing the plate, and it snaps in the middle (centerline of the bolt), vertically. Stiffening that plate so it resists that bowing is what you want/need. You can do that by increasing the thickness. You could do that by laminating more 1/16th layers- which would add weight, of course. You could get a LOT more stiffness, at the same or lower weight than you’re now running, by “end grain sandwich” laminated construction – from the wall, going out, 1/64th birch plywood (which you can get at Ace Hardware, in their hobby woods bin), then 15/32nds of light balsa, arranged so the grain is running perpendicular to the wall, then an outer layer of the 1/64th plywood. Total thickness is then 1/2". If you keep total thickness at/just under ½ inch, the commercial plywood is fine/legal. The “box” cross section you create when you laminate these 3 layers together like this will be A LOT stiffer than your 3/16ths lam- a lot. The second advantage that thicker cross section will give you is glue area- the surface area available for glue to hold the tension member(s) in the base/plate. When you get the base/plate thick enough to hold higher load, the next issue you’ll run into is the glue joints of the tension member in the base shearing; the larger the glue area, the higher load it can handle without shearing failure.
Last edited by Balsa Man on November 30th, 2012, 8:41 pm, edited 1 time in total.
Len Joeris
Fort Collins, CO
Fort Collins, CO
Re: Boomilever B/C
Is this step needed if only 1 bolt is used?Balsa Man wrote:A cross line on the bolt line is marked 10cm to either side of center- a center and the two side bolt holes are drilled.
-
- Coach
- Posts: 1318
- Joined: November 13th, 2008, 3:01 am
- Division: C
- State: CO
- Has thanked: 0
- Been thanked: 3 times
Re: Boomilever B/C
Nope- described that way to cover folk using 2 bolts. If you're using one. you just want to make sure the boom arm line is lined up directly under it.jma wrote:Is this step needed if only 1 bolt is used?Balsa Man wrote:A cross line on the bolt line is marked 10cm to either side of center- a center and the two side bolt holes are drilled.
Len Joeris
Fort Collins, CO
Fort Collins, CO
Re: Boomilever B/C
Thanks Balsa Man.Balsa Man wrote:Nope- described that way to cover folk using 2 bolts. If you're using one. you just want to make sure the boom arm line is lined up directly under it.jma wrote:Is this step needed if only 1 bolt is used?Balsa Man wrote:A cross line on the bolt line is marked 10cm to either side of center- a center and the two side bolt holes are drilled.
But can you explain more about what you mean in that last sentence?
-
- Coach
- Posts: 1318
- Joined: November 13th, 2008, 3:01 am
- Division: C
- State: CO
- Has thanked: 0
- Been thanked: 3 times
Re: Boomilever B/C
It's just that whichever single hole you use, the compression member/"boom arm" needs to be directly under the bolt hole the tension member(s)- and the jig needs to be set up to give you that alignment. That's all.
Len Joeris
Fort Collins, CO
Fort Collins, CO
Re: Boomilever B/C
Thanks.Balsa Man wrote:It's just that whichever single hole you use, the compression member/"boom arm" needs to be directly under the bolt hole the tension member(s)- and the jig needs to be set up to give you that alignment. That's all.
Who is online
Users browsing this forum: No registered users and 1 guest