Wright Stuff C
-
- Member
- Posts: 829
- Joined: June 16th, 2013, 12:35 pm
- Division: C
- State: MI
- Has thanked: 0
- Been thanked: 39 times
Re: Wright Stuff C
Lechassin,
Yes, I agree. Moving the CG forward and adding a degree or two of decalage is a logical next change to improve pitch stability.
You'll probably find that you only need to move CG forward 1/8" or so.
Several years ago the rules specified a small wing and we ended up flying with 45% SSM! Flew some of the best times in the nation that year with that strange setup.
Brian T
Yes, I agree. Moving the CG forward and adding a degree or two of decalage is a logical next change to improve pitch stability.
You'll probably find that you only need to move CG forward 1/8" or so.
Several years ago the rules specified a small wing and we ended up flying with 45% SSM! Flew some of the best times in the nation that year with that strange setup.
Brian T
Re: Wright Stuff C
We don't mind answering. We just want the highest time we can get, with no expectation of going past our local meets (the rest of our events won't advance so AFAIK Wright Stuff won't either).
The prop: it consists of a hub, three spokes, and three blades. Currently the hub is two 3/8" discs of balsa that sandwich three spokes made of thin paper clip with a bend on the ends to keep them from twisting. The whole hub is soaked in thin CA to reinforce it. Our drive shaft is a piece of tiny threaded wire. I think you'd be OK with a bent music wire shaft but you'd need to work out how to change the prop without affecting the thrust line. Our best blades are cut from the one red SOLO cup we had, but we can't find more without ribs molded into them, so we're also using yogurt pots. The SOLO plastic takes CA well and doesn't need to be pre-sanded, so I'm looking for more. The blades are cut on a 45 degree bias from the cup so that the root pitch is higher than the tip pitch. They are glued with thick CA, then reinforced with a tiny piece of fiberglass cloth soaked in thin CA to keep them from popping off from an impact (I bet you could even use paper towel, anything fibrous and thin). We pinch the cloth down with a shield of plastic baggy that peels off when the glue is cured. We then twist the spokes to get 30 degrees pitch at the tip (about 45 degrees at the root). We use the jig we made but a simple template would work. We're still looking for the best blade setup. In the videos, the blades are about 3/4" chord and as long as possible to get the maximum 8cm diameter, the tips are a bit more than 30 degrees (increased so the knots don't run out). We use a template with an 8cm hole in it to slowly shape the tips until the prop drops through. At first we spent time getting exactly 120 degrees between each spoke and balanced the props with dabs of thick CA on the lightest blades, but we don't bother any more. Even though our prop spins at almost 3000 rpm (3000 turns used in 70 seconds), the prop is light and doesn't shake the plane even if it's imperfect.
The fences: they are in lieu of dihedral and they double as upper wing braces. I (Dad) am proud to have thought of that and I think it yields, simple, durable wings that cannot warp (I hesitate to say better than the kit produced by the F1D champ
). The prototype had fences only on the lower wing but roll stability was marginal so we added two more. Each fence is 3 cm high and that was just a good guess. Bigger would just weigh more.
The rudder: our prototype's was bigger but tiny changes in the setting would produce too much effect, so we reduced the rudder size to fix that. Less weight out back also means a longer tail boom which helps the stab.
Wing and stab posts weigh more than zero, so we omitted them in spite of their known advantages. The upper wing is on posts so that yields some of the effect. Our theory is that every milligram we can spare should be allocated to the longest possible motor stick without exceeding the 8.0 gram total. In fact I recommend you make frail wings, fences, stab, rudder, tail boom, and prop assembly, then see what's left over for the motor stick. The thinner the stick is without bowing, the longer it will be. Ours is 1/4" (tapered to 1/8" at the ends) x 3/32" x 18". It will bow to the right or left under load IF the plane is held on its side, but it will stay straight if the plane is flat, it's that close to the limit.
As for the frail airframe, it's stiff enough to stay straight, but we can see it deform when it hits anything, which I think is good. The prototype used thicker/harder wood and glue joints would pop free from impacts. In our case, aft CG plus a good hit can cause a high power nose-dive straight down into the floor with no damage at all, not even the prop.
Brian, thanks for the suggestion; we advanced the CG 1/8" on one plane by moving the tiny weight to the leading edge, and on the other we had to shorten the tail boom 1"
. We'll tweak the stab as needed this weekend.
The prop: it consists of a hub, three spokes, and three blades. Currently the hub is two 3/8" discs of balsa that sandwich three spokes made of thin paper clip with a bend on the ends to keep them from twisting. The whole hub is soaked in thin CA to reinforce it. Our drive shaft is a piece of tiny threaded wire. I think you'd be OK with a bent music wire shaft but you'd need to work out how to change the prop without affecting the thrust line. Our best blades are cut from the one red SOLO cup we had, but we can't find more without ribs molded into them, so we're also using yogurt pots. The SOLO plastic takes CA well and doesn't need to be pre-sanded, so I'm looking for more. The blades are cut on a 45 degree bias from the cup so that the root pitch is higher than the tip pitch. They are glued with thick CA, then reinforced with a tiny piece of fiberglass cloth soaked in thin CA to keep them from popping off from an impact (I bet you could even use paper towel, anything fibrous and thin). We pinch the cloth down with a shield of plastic baggy that peels off when the glue is cured. We then twist the spokes to get 30 degrees pitch at the tip (about 45 degrees at the root). We use the jig we made but a simple template would work. We're still looking for the best blade setup. In the videos, the blades are about 3/4" chord and as long as possible to get the maximum 8cm diameter, the tips are a bit more than 30 degrees (increased so the knots don't run out). We use a template with an 8cm hole in it to slowly shape the tips until the prop drops through. At first we spent time getting exactly 120 degrees between each spoke and balanced the props with dabs of thick CA on the lightest blades, but we don't bother any more. Even though our prop spins at almost 3000 rpm (3000 turns used in 70 seconds), the prop is light and doesn't shake the plane even if it's imperfect.
The fences: they are in lieu of dihedral and they double as upper wing braces. I (Dad) am proud to have thought of that and I think it yields, simple, durable wings that cannot warp (I hesitate to say better than the kit produced by the F1D champ
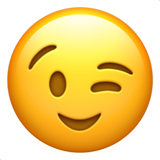
The rudder: our prototype's was bigger but tiny changes in the setting would produce too much effect, so we reduced the rudder size to fix that. Less weight out back also means a longer tail boom which helps the stab.
Wing and stab posts weigh more than zero, so we omitted them in spite of their known advantages. The upper wing is on posts so that yields some of the effect. Our theory is that every milligram we can spare should be allocated to the longest possible motor stick without exceeding the 8.0 gram total. In fact I recommend you make frail wings, fences, stab, rudder, tail boom, and prop assembly, then see what's left over for the motor stick. The thinner the stick is without bowing, the longer it will be. Ours is 1/4" (tapered to 1/8" at the ends) x 3/32" x 18". It will bow to the right or left under load IF the plane is held on its side, but it will stay straight if the plane is flat, it's that close to the limit.
As for the frail airframe, it's stiff enough to stay straight, but we can see it deform when it hits anything, which I think is good. The prototype used thicker/harder wood and glue joints would pop free from impacts. In our case, aft CG plus a good hit can cause a high power nose-dive straight down into the floor with no damage at all, not even the prop.
Brian, thanks for the suggestion; we advanced the CG 1/8" on one plane by moving the tiny weight to the leading edge, and on the other we had to shorten the tail boom 1"
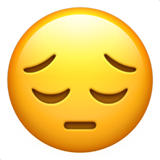
-
- Member
- Posts: 829
- Joined: June 16th, 2013, 12:35 pm
- Division: C
- State: MI
- Has thanked: 0
- Been thanked: 39 times
Re: Wright Stuff C
Lechassin,
Glad to pass on ideas. 1/8" changes in CG made a noticeable difference with our design.
The tiny stab appears to make the airplane very sensitive to small pitch trim changes.
I'm sure you have it in your plans, but definitely wind your rubber motors more aggressively. We use John Barker's (R.I.P.) formula for estimating maximum turns. Works pretty well. If you need it, I can try to find a way to post. It's also in several different Hip Pocket threads.
Brian T
Glad to pass on ideas. 1/8" changes in CG made a noticeable difference with our design.
The tiny stab appears to make the airplane very sensitive to small pitch trim changes.
I'm sure you have it in your plans, but definitely wind your rubber motors more aggressively. We use John Barker's (R.I.P.) formula for estimating maximum turns. Works pretty well. If you need it, I can try to find a way to post. It's also in several different Hip Pocket threads.
Brian T
Re: Wright Stuff C
Lol, I thought we just wind a motor till it breaks, note the number of turns, and multiply by 0.85 or 0.9. What's the better formula?
Our lubed 1/16" test piece of rubber broke at 105 turns per inch, so we figured a 32" motor will break at about 3360 turns. We are washing, lubing, and stretching the rubber while we wind, but we are not sourcing any particular vintage rubber. I am curious to know what the best 1/16" rubber gets per inch.
90% puts us at a little over 3000 turns and we're needing to exceed that briefly (3150 then go down 150) to avoid contact with even the lowest obstacles. We still break the motors eventually. At about 3000 rpm, even going to 100% with the last 360 turns would only add about 12% to our 65 seconds, or another 8 seconds or so. Therefore I don't think there's a two minute flight to be had by taking risks with our undated rubber.
Hopefully we can get good improvements by slowing the prop down at launch, using big low pitched blades and allowing them to flare at high rpm. We just ordered some un-ribbed SOLO cups off EBay of all places, then we can get to building more props.
Our family has hunters and we have access to a [German] laser range-finder that we hope is precise enough to mark our torque meter for different ceiling heights. Our goal is to zap the ceiling of whatever venue we encounter and reduce or eliminate the need for test flights.
Our lubed 1/16" test piece of rubber broke at 105 turns per inch, so we figured a 32" motor will break at about 3360 turns. We are washing, lubing, and stretching the rubber while we wind, but we are not sourcing any particular vintage rubber. I am curious to know what the best 1/16" rubber gets per inch.
90% puts us at a little over 3000 turns and we're needing to exceed that briefly (3150 then go down 150) to avoid contact with even the lowest obstacles. We still break the motors eventually. At about 3000 rpm, even going to 100% with the last 360 turns would only add about 12% to our 65 seconds, or another 8 seconds or so. Therefore I don't think there's a two minute flight to be had by taking risks with our undated rubber.
Hopefully we can get good improvements by slowing the prop down at launch, using big low pitched blades and allowing them to flare at high rpm. We just ordered some un-ribbed SOLO cups off EBay of all places, then we can get to building more props.
Our family has hunters and we have access to a [German] laser range-finder that we hope is precise enough to mark our torque meter for different ceiling heights. Our goal is to zap the ceiling of whatever venue we encounter and reduce or eliminate the need for test flights.
-
- Member
- Posts: 829
- Joined: June 16th, 2013, 12:35 pm
- Division: C
- State: MI
- Has thanked: 0
- Been thanked: 39 times
Re: Wright Stuff C
Lechassin,
Maybe you're already doing this, but it's best to measure rubber in density in grams/inch rather than thickness. Companies that sell bulk cut rubber, out of necessity, need to sell in "width". However, the stock they are cutting from varies both in thickness and in density and this variance can be as much as 3-5%. This is enough variance to make an airplane that tests at under the girders with one loop of rubber go through the rafters with another loop (if width measured).
A 32" loop of average density 1/16" wide (.04165 g/in) tan ss will should take quite a bit more than 3,360 turns before breaking if lubed well, broken in, stretched to 7x relaxed length during winding and about 60% turns at full stretch and remaining turns while walking towards the torque meter (monitoring torque continuously). Usually, a motor will take this higher turn count on the second or third use.
Brian T
Maybe you're already doing this, but it's best to measure rubber in density in grams/inch rather than thickness. Companies that sell bulk cut rubber, out of necessity, need to sell in "width". However, the stock they are cutting from varies both in thickness and in density and this variance can be as much as 3-5%. This is enough variance to make an airplane that tests at under the girders with one loop of rubber go through the rafters with another loop (if width measured).
A 32" loop of average density 1/16" wide (.04165 g/in) tan ss will should take quite a bit more than 3,360 turns before breaking if lubed well, broken in, stretched to 7x relaxed length during winding and about 60% turns at full stretch and remaining turns while walking towards the torque meter (monitoring torque continuously). Usually, a motor will take this higher turn count on the second or third use.
Brian T
Re: Wright Stuff C
We were stretching only 2-3 times relaxed length and coming in too soon. A 5% change in density translates to a 5% change in maximum winds? If so, I'll properly wind a lightly used 32" motor to breaking and extrapolate accordingly. For now we're using motors right away and until they break, but as we get closer to final specs, we'll use a motor after 1- 2 break-in winds.
They seem to deteriorate quickly; how many times can a motor be fully wound and be expected to be reasonably consistent? Can that be repeated on subsequent days and if so, about how many?
We are going to move the wings aft 1/8" to bring the CG back to the perfect middle of the hook-to-hook distance, and we are going to shift the wings left 1/4" to even out the banking angle during right and left turns. In the videos we noticed that prop torque is causing a slightly higher banking angle going left so the climb rate is a little lower. Our goal is circles that are the same size and shape with identical climb rates going either way, with only a rudder change.
They seem to deteriorate quickly; how many times can a motor be fully wound and be expected to be reasonably consistent? Can that be repeated on subsequent days and if so, about how many?
We are going to move the wings aft 1/8" to bring the CG back to the perfect middle of the hook-to-hook distance, and we are going to shift the wings left 1/4" to even out the banking angle during right and left turns. In the videos we noticed that prop torque is causing a slightly higher banking angle going left so the climb rate is a little lower. Our goal is circles that are the same size and shape with identical climb rates going either way, with only a rudder change.
-
- Member
- Posts: 829
- Joined: June 16th, 2013, 12:35 pm
- Division: C
- State: MI
- Has thanked: 0
- Been thanked: 39 times
Re: Wright Stuff C
Lechassin,
Each 1/8" shift forward increases SSM about 4%. It's possible more than 1/8" will be needed (a long with increased decalage, of course). We did see noticable improvements with the first 1/8" change.
I don't think density change and turn count are linear, I'll need to look at the equation.
Brian T
Each 1/8" shift forward increases SSM about 4%. It's possible more than 1/8" will be needed (a long with increased decalage, of course). We did see noticable improvements with the first 1/8" change.
I don't think density change and turn count are linear, I'll need to look at the equation.
Brian T
Re: Wright Stuff C
On your winding advice a 32" motor broke at a much higher 4200 turns, so we'll aim for 3750 and back off to whatever torque the ceiling will permit. The motor stick is still straight with all those knots so we got lucky; we didn't build the plane with that much load in mind.
Moving the wings to the left 3mm on our "test plane" flattened left turns nicely (with partial winding) and reduced right rudder to almost nothing for nice right turn, with slight right banking. Maybe we'll bring the wings back a tad, but we'll try the plane at full torque first.
We'll also adjust CG and decalage more as needed.
Moving the wings to the left 3mm on our "test plane" flattened left turns nicely (with partial winding) and reduced right rudder to almost nothing for nice right turn, with slight right banking. Maybe we'll bring the wings back a tad, but we'll try the plane at full torque first.
We'll also adjust CG and decalage more as needed.
-
- Member
- Posts: 256
- Joined: February 25th, 2007, 9:54 pm
- Has thanked: 0
- Been thanked: 0
Re: Wright Stuff C
Brian T gave excellent advice in his post yesterday about how to wind a rubber motor for an indoor duration model airplane. Experts go by the length and weight of a rubber motor, and not its width and weight. The thickness and density of commercial rubber varies along its length. Also, it is not possible to strip the width of rubber with a high degree of uniformity and precision.
In my experience (approximately 15 years of flying indoors) I have found that I get the best flights on the 2nd through 4th winds of a given rubber motor. After that the performance of the rubber motor gradually declines in terms of the flight times that I can achieve with the same rubber motor. Depending on the batch of rubber, sometimes a rubber motor that has been wound hard five or six times can “rest” and can produce good flight times weeks or months later. I would not use such a used rubber motor in a WS competition. I save used rubber motors if they have been made from a particular batch of rubber known in the free flight community to be outstanding in terms of performance.
lechassin - I am extremely impressed by your dedication and rapid advancement under very challenging WS rules.
In my experience (approximately 15 years of flying indoors) I have found that I get the best flights on the 2nd through 4th winds of a given rubber motor. After that the performance of the rubber motor gradually declines in terms of the flight times that I can achieve with the same rubber motor. Depending on the batch of rubber, sometimes a rubber motor that has been wound hard five or six times can “rest” and can produce good flight times weeks or months later. I would not use such a used rubber motor in a WS competition. I save used rubber motors if they have been made from a particular batch of rubber known in the free flight community to be outstanding in terms of performance.
lechassin - I am extremely impressed by your dedication and rapid advancement under very challenging WS rules.
Last edited by calgoddard on September 25th, 2019, 7:47 am, edited 1 time in total.
Re: Wright Stuff C
Confession: lechassin is my son Luke, I'm Eric the Dad. He hasn't built yet this year, he's winding, launching, observing performance, and trimming. I rationalize this because we aren't using a kit designed by an F1D champ and delivered to our door pre-developed. I think what we're doing is better, because while the rules do allow kits, they also say we should be designing the plane. To me that precludes kits entirely, but if other kids can buy a design, then I think it's fair that I give my boy a design *dons flame suit*.
The rubber inconsistency and rapid deterioration: one break-in run and three flights for an all-day trim/practice session means a LOT of rubber
but I don't see how one could get good trim information with a motor that loses power each subsequent flight.
The rubber inconsistency and rapid deterioration: one break-in run and three flights for an all-day trim/practice session means a LOT of rubber
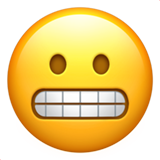
Who is online
Users browsing this forum: No registered users and 0 guests