No rules about maximum/minimum heights of bridges, though it is used as a second tiebreaker. One issue I encountered when making my bridges taller while still trying to maintain a low mass was that all my members were longer and less dense so they buckled more. So far my best efficiencies are from my 10cm tall bridges (I've tested bridges from 10cm tall to 17cm tall).iwonder wrote:Ahh the lengths I went to trying to get high speed footage of my structures breaking....Friedoyster3 wrote: The structure isn't so much twisting and breaking as it is deforming downwards. Across the entire span the deformation is actually quite noticeable. But since the break patterns aren't very conclusive, I can't really be 100% sure that's all that is happening to cause failure without high speed footage.
From how it sounds you could probably try horizontal braces, if the whole thing deforms try making it taller (I haven't read the rules enough to know if you can...?)
Designs B/C
- bernard
- Administrator
- Posts: 2493
- Joined: January 5th, 2014, 3:12 pm
- Division: Grad
- State: WA
- Pronouns: He/Him/His
- Has thanked: 184 times
- Been thanked: 780 times
- Contact:
Re: Designs B/C
"One of the ways that I believe people express their appreciation to the rest of humanity is to make something wonderful and put it out there." – Steve Jobs
-
- Admin Emeritus
- Posts: 1115
- Joined: May 10th, 2011, 8:25 pm
- Division: Grad
- State: TX
- Has thanked: 0
- Been thanked: 1 time
Re: Designs B/C
Yeah, I think in his case though if the bridge is indeed folding, it might help to make it a little taller and a little heavier. The longer members would have to more dense so they don't buckle as easily, which means it will be heavier. But since it's taller it also is less prone to folding up.bernard wrote:No rules about maximum/minimum heights of bridges, though it is used as a second tiebreaker. One issue I encountered when making my bridges taller while still trying to maintain a low mass was that all my members were longer and less dense so they buckled more. So far my best efficiencies are from my 10cm tall bridges (I've tested bridges from 10cm tall to 17cm tall).
'If you're the smartest person in the room, you're in the wrong room' - Unknown
-
- Member
- Posts: 99
- Joined: February 1st, 2009, 6:38 am
- Division: C
- State: IN
- Has thanked: 0
- Been thanked: 0
Re: Designs B/C
I have not yet tried increasing the height of the bridge, but it is definitely on my upcoming list of design variations. One thing to keep in mind though is that there is a sort of "ideal" proportion between span length and height of the bridge, and I believe that it is close to 6:1 (span:height).
Over the past few weeks the most successful change I've made has been improving the lateral bracing. So if anyone finds that they are having a similar problem as I was, I highly recommend that change.
The bridge I tested yesterday at regionals with these improvements tested at a highly respectable efficiency, so I think I'm headed in the right direction. What I can't be 100% sure on is whether that score is a result of my using stiffer wood knowing that it would be a competition bridge, or if the improvement in score was due to improved design. I suspect a combination of the two.
My question for you all therefore becomes what are some of the best ways to "quality control" balsa wood? Specifically for stiffness. I know that there is an approximate correlation between stiffness and density, but this rule is in no way set in stone. How should one go about finding the lightest, stiffest wood? Are there any accurate and repeatable stiffness tests other than just by feel?
Over the past few weeks the most successful change I've made has been improving the lateral bracing. So if anyone finds that they are having a similar problem as I was, I highly recommend that change.
The bridge I tested yesterday at regionals with these improvements tested at a highly respectable efficiency, so I think I'm headed in the right direction. What I can't be 100% sure on is whether that score is a result of my using stiffer wood knowing that it would be a competition bridge, or if the improvement in score was due to improved design. I suspect a combination of the two.
My question for you all therefore becomes what are some of the best ways to "quality control" balsa wood? Specifically for stiffness. I know that there is an approximate correlation between stiffness and density, but this rule is in no way set in stone. How should one go about finding the lightest, stiffest wood? Are there any accurate and repeatable stiffness tests other than just by feel?
University of Michigan Aerospace Engineering
Munster High School, Indiana
2015 Nationals: Bridge 12th; Air Traj 7th; Scrambler 6th; Geo Maps 5th; Team 6th!
"Science Olympiad is, was, and always will be one of the greatest things that ever happened to me."
Munster High School, Indiana
2015 Nationals: Bridge 12th; Air Traj 7th; Scrambler 6th; Geo Maps 5th; Team 6th!
"Science Olympiad is, was, and always will be one of the greatest things that ever happened to me."
-
- Admin Emeritus
- Posts: 1115
- Joined: May 10th, 2011, 8:25 pm
- Division: Grad
- State: TX
- Has thanked: 0
- Been thanked: 1 time
Re: Designs B/C
I'm assuming that you're using sheets of balsa and cutting them into the pieces you need, which tends to be a lot more consistent than simply using sticks. Beyond the same weight, I don't remember ever hearing of something else people do. I know that there's a few different devices out there to test tension, compression, and stiffness (I build a compression testing rig for boom at one point), and I guess you could take samples of the material and test those, but as far as non-destructive testing of wood I'm not quite sure. You might be able to just hang a small mass on the piece and see how far it bends if you're careful. (but honestly, if you're not looking at a top maybe 15 spot at nationals then weight is more than enough, anyways, stiffness would only apply to members in compression so...)Friedoyster3 wrote:I have not yet tried increasing the height of the bridge, but it is definitely on my upcoming list of design variations. One thing to keep in mind though is that there is a sort of "ideal" proportion between span length and height of the bridge, and I believe that it is close to 6:1 (span:height).
Over the past few weeks the most successful change I've made has been improving the lateral bracing. So if anyone finds that they are having a similar problem as I was, I highly recommend that change.
The bridge I tested yesterday at regionals with these improvements tested at a highly respectable efficiency, so I think I'm headed in the right direction. What I can't be 100% sure on is whether that score is a result of my using stiffer wood knowing that it would be a competition bridge, or if the improvement in score was due to improved design. I suspect a combination of the two.
My question for you all therefore becomes what are some of the best ways to "quality control" balsa wood? Specifically for stiffness. I know that there is an approximate correlation between stiffness and density, but this rule is in no way set in stone. How should one go about finding the lightest, stiffest wood? Are there any accurate and repeatable stiffness tests other than just by feel?
I think I see where you're getting the 1/6th number from, but in reality it could be different, so it's worth a shot.
'If you're the smartest person in the room, you're in the wrong room' - Unknown
- bernard
- Administrator
- Posts: 2493
- Joined: January 5th, 2014, 3:12 pm
- Division: Grad
- State: WA
- Pronouns: He/Him/His
- Has thanked: 184 times
- Been thanked: 780 times
- Contact:
Re: Designs B/C
Ideal span-to-height ratio:Friedoyster3 wrote:I have not yet tried increasing the height of the bridge, but it is definitely on my upcoming list of design variations. One thing to keep in mind though is that there is a sort of "ideal" proportion between span length and height of the bridge, and I believe that it is close to 6:1 (span:height).
Over the past few weeks the most successful change I've made has been improving the lateral bracing. So if anyone finds that they are having a similar problem as I was, I highly recommend that change.
The bridge I tested yesterday at regionals with these improvements tested at a highly respectable efficiency, so I think I'm headed in the right direction. What I can't be 100% sure on is whether that score is a result of my using stiffer wood knowing that it would be a competition bridge, or if the improvement in score was due to improved design. I suspect a combination of the two.
My question for you all therefore becomes what are some of the best ways to "quality control" balsa wood? Specifically for stiffness. I know that there is an approximate correlation between stiffness and density, but this rule is in no way set in stone. How should one go about finding the lightest, stiffest wood? Are there any accurate and repeatable stiffness tests other than just by feel?
Garrett's Bridges wrote:I was once told that the optimal height for an arch bridge is 1/6th the length of the span. That means if your bridge is 6 inches long, it should be 1 inch tall. My experience has confirmed that this is a very good starting place for an arch bridge. And I believe the same ratio of height to length can be applied to regular truss bridges. Link.
This video shows one way of measuring wood stiffness. I found another link that describes the same approach.Optimal design of through-truss steel bridges wrote:The optimum height-to-span ratio for through-truss steel bridges of medium span falls within the range of 1/7 and 1/10 for two traffic lanes and between 1/8 and 1/12 for a single lane, irrespective of deck type. Link.
Euler Buckling Method for Calculating Youngs Modulus and Stiffness Coefficient wrote:I am afraid it is not enough simply to weigh it and calculate the density as most of it is has poor mechanical properties. I now test the wood for Youngs modulus right there in the shop and only take the stuff that has the right density and stiffness. There are several ways of measuring wood stiffness but the one I prefer uses Euler buckling and only takes a few seconds if you have a programmable pocket computer to calculate the results. With this method, you hold the sheet vertically on a digital kitchen scale and then press on the top end until the sheet buckles sideways - you calculate the properties of the wood from its dimensions, weight and the buckling load.
"One of the ways that I believe people express their appreciation to the rest of humanity is to make something wonderful and put it out there." – Steve Jobs
-
- Member
- Posts: 676
- Joined: July 25th, 2012, 5:04 pm
- Division: Grad
- State: FL
- Has thanked: 0
- Been thanked: 0
Re: Designs B/C
Our teams are using a very simplistic bridge design that we saw in Orlando last year. A computer modeling came out with 10 cm height as a practical minimum. Going up from there added a little bit of efficiency. HS is using 12 cm and is running about 2,000 for a score. Lighter and smaller balsa is currently being tried. Gluing has been most of the problem so far.
There are several sites that talk about testing bend strength. Most want to sell a tester. Remember, If you are using A/C grain wood, one side will test higher than the other.
There are several sites that talk about testing bend strength. Most want to sell a tester. Remember, If you are using A/C grain wood, one side will test higher than the other.
-
- Admin Emeritus
- Posts: 1115
- Joined: May 10th, 2011, 8:25 pm
- Division: Grad
- State: TX
- Has thanked: 0
- Been thanked: 1 time
Re: Designs B/C
But that must mean it's a boring old square piece!retired1 wrote:Remember, If you are using A/C grain wood, one side will test higher than the other.
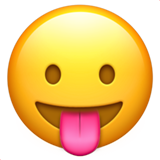
'If you're the smartest person in the room, you're in the wrong room' - Unknown
-
- Member
- Posts: 676
- Joined: July 25th, 2012, 5:04 pm
- Division: Grad
- State: FL
- Has thanked: 0
- Been thanked: 0
Re: Designs B/C
Testing a sheet is only a starting point as normally there is a good bit of difference in the individual sticks cut from that sheet.
In direct compression, a square is the optimal shape. Not so in tension.
In direct compression, a square is the optimal shape. Not so in tension.
-
- Admin Emeritus
- Posts: 1115
- Joined: May 10th, 2011, 8:25 pm
- Division: Grad
- State: TX
- Has thanked: 0
- Been thanked: 1 time
Re: Designs B/C
Well if you must be technical, a cylindrical member would be better in compression, and yes, it has been done before.retired1 wrote:Testing a sheet is only a starting point as normally there is a good bit of difference in the individual sticks cut from that sheet.
In direct compression, a square is the optimal shape. Not so in tension.
'If you're the smartest person in the room, you're in the wrong room' - Unknown
-
- Coach
- Posts: 573
- Joined: February 6th, 2006, 2:20 pm
- Division: B
- Has thanked: 0
- Been thanked: 7 times
Re: Designs B/C
actually, both are correct... Cylinders provide thew best overall efficiency, but they are unpredictable as to which direction they will buckle. Squares are not quite as efficient, but you only need to brace them in 2 planes, so what is lost by going to the square may be gained back in the bracing... depends on the individual situation.
Dan Holdgreve
Northmont Science Olympiad
Dedicated to the Memory of Len Joeris
"For the betterment of Science"
Northmont Science Olympiad
Dedicated to the Memory of Len Joeris
"For the betterment of Science"
Who is online
Users browsing this forum: No registered users and 0 guests