So in a bridge, the gusset would fit flush against the tension and compression members? Would that be the same thing as adding extra layers onto the distal end for boomilevers? Would it be better it add it on the underside or on the exterior of the bridge?nxtscholar wrote:This image is actually from the Wright Stuff guide, but it serves it's purpose. Notice that the 2nd and 4th configurations both have a small triangular plate, but one is more effective than the other. btw, UQOnyx, I take it that you did stay behind with your MS team then?
@taimur18: In a rather heinous oversimplification, bass is stronger, but inherently heavier; balsa is weaker, but much lighter. You have to figure out which areas are subject to greater compression/tension and decide whether or not to use bass/balsa. There are numerous programs out there like JHU's bridge builder program that can help you calculate the force exerted on each member.
Designs B/C
-
- Member
- Posts: 70
- Joined: March 14th, 2012, 3:13 pm
- Division: C
- State: NJ
- Has thanked: 0
- Been thanked: 0
Re: Designs B/C
-
- Admin Emeritus
- Posts: 1115
- Joined: May 10th, 2011, 8:25 pm
- Division: Grad
- State: TX
- Has thanked: 0
- Been thanked: 1 time
Re: Designs B/C
I'm not actually sure if those are the best for load bearing structures. Just for example, 'bad' or 'better' will probably be stronger in compression, when the vertical member is pushed up into the horizontal member, than 'good' or 'best' because the load is evenly distributed along the end area of the wood, rather than being concentrated on one side of a rather thick piece. (not to mention the fact that there's no stress on the glue joint in that scenario).
In tension, 'better' with gussets on both sides will probably be best because it gives the most contact area between the gusset and the vertical member, depending on the grain in the gusset. Again, 'good' and 'best' in tension would twist a tiny fraction, but more importantly the shear stress is concentrated on one side of members instead of on multiple sides. In this case though, 'bad' is, in fact, horrible.
The major thing to keep in mind is that you need to maximize the surface area that's in contact and keep the loads evenly distributed around the members (as much as possible). End grain joints are generally worse, which is why gussets are used in the case of 'better', then the gusset carries most of the load, and it has contact with the 'side' grain in both pieces, so as long as the grain in your gusset runs in the direction of the applied force, it should be just fine.
In tension, 'better' with gussets on both sides will probably be best because it gives the most contact area between the gusset and the vertical member, depending on the grain in the gusset. Again, 'good' and 'best' in tension would twist a tiny fraction, but more importantly the shear stress is concentrated on one side of members instead of on multiple sides. In this case though, 'bad' is, in fact, horrible.
The major thing to keep in mind is that you need to maximize the surface area that's in contact and keep the loads evenly distributed around the members (as much as possible). End grain joints are generally worse, which is why gussets are used in the case of 'better', then the gusset carries most of the load, and it has contact with the 'side' grain in both pieces, so as long as the grain in your gusset runs in the direction of the applied force, it should be just fine.
'If you're the smartest person in the room, you're in the wrong room' - Unknown
-
- Member
- Posts: 18
- Joined: January 26th, 2015, 5:38 pm
- Division: C
- State: NC
- Has thanked: 0
- Been thanked: 0
Re: Designs B/C
Just a quick question, how heavy is too heavy a bridge? Like ours weighs like 16 but holds 13 kilos. I know not a great score but our school isn't very old. This is my first post 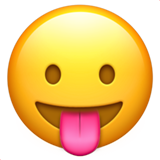
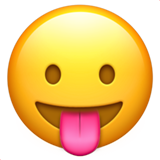
Self-actualization is an irony, for when you achieve it, you realize you have not achieved it.
- bernard
- Administrator
- Posts: 2495
- Joined: January 5th, 2014, 3:12 pm
- Division: Grad
- State: WA
- Pronouns: He/Him/His
- Has thanked: 184 times
- Been thanked: 783 times
- Contact:
Re: Designs B/C
I think your bridge isn't too heavy. As you improve your bridge design, if it starts holding much more than 15 kg, then your bridge has extra wood that isn't needed. I had a bridge that was about 10 grams and held 20 kg, so it could lose some wood to improve the efficiency. Pay attention to which members seem to never break. If your tension always breaks, of course don't take wood away from the tension.IvySpear wrote:Just a quick question, how heavy is too heavy a bridge? Like ours weighs like 16 but holds 13 kilos. I know not a great score but our school isn't very old. This is my first post
"One of the ways that I believe people express their appreciation to the rest of humanity is to make something wonderful and put it out there." – Steve Jobs
-
- Coach
- Posts: 573
- Joined: February 6th, 2006, 2:20 pm
- Division: B
- Has thanked: 0
- Been thanked: 7 times
Re: Designs B/C
At the Magsig OH invitational last Saturday, the bridges ranged from 5 grams to over 50 grams, and carried everything from just the bucket to full load... For this being your first year, first attempt you should be very proud of a 16 gram bridge carrying nearly the full load... Keep in mind, there is no penalty for not carrying the full load... there is no bonus for doing so... That being said, the theoretical goal here should be for total destruction at 14.99 grams, with every part failing at the same time... You are not that far off carrying what you need to, now just work on locating the "dead wood." pieces that are either not providing any meaningful structural reinforcement, or are oversized for the needs. By finding these areas your bridge weight will continue to drop, and your scores will skyrocket... assuming you can maintain carrying that load.IvySpear wrote:Just a quick question, how heavy is too heavy a bridge? Like ours weighs like 16 but holds 13 kilos. I know not a great score but our school isn't very old. This is my first post
Dan Holdgreve
Northmont Science Olympiad
Dedicated to the Memory of Len Joeris
"For the betterment of Science"
Northmont Science Olympiad
Dedicated to the Memory of Len Joeris
"For the betterment of Science"
-
- Member
- Posts: 99
- Joined: February 1st, 2009, 6:38 am
- Division: C
- State: IN
- Has thanked: 0
- Been thanked: 0
Re: Designs B/C
A question about lateral bracing:
I've been constructing my lateral bracing on top of the compression member compression member like figure 1 below. However the last three bridges I've built have all failed along the compression member at the yellow circle. Which got me thinking, maybe I should try to do something like the second option to prevent a buckling failure of the compression member at near that type of node. What do you all think about this?
I've also been considering option III, which requires the lateral bracing to cross over one another with some really weird torques on the pieces. How should I go about constructing that? The one time that I tried option III, the two trusses separated without breaking because the lateral bracing connections at the nodes were too weak. Any ideas?
(This view is top down and does not represent the entire span, just a small section. Brown sticks are the compression members, red rectangles are truss nodes that extend into the screen, and blue sticks are lateral bracing.)
I've been constructing my lateral bracing on top of the compression member compression member like figure 1 below. However the last three bridges I've built have all failed along the compression member at the yellow circle. Which got me thinking, maybe I should try to do something like the second option to prevent a buckling failure of the compression member at near that type of node. What do you all think about this?
I've also been considering option III, which requires the lateral bracing to cross over one another with some really weird torques on the pieces. How should I go about constructing that? The one time that I tried option III, the two trusses separated without breaking because the lateral bracing connections at the nodes were too weak. Any ideas?
(This view is top down and does not represent the entire span, just a small section. Brown sticks are the compression members, red rectangles are truss nodes that extend into the screen, and blue sticks are lateral bracing.)
University of Michigan Aerospace Engineering
Munster High School, Indiana
2015 Nationals: Bridge 12th; Air Traj 7th; Scrambler 6th; Geo Maps 5th; Team 6th!
"Science Olympiad is, was, and always will be one of the greatest things that ever happened to me."
Munster High School, Indiana
2015 Nationals: Bridge 12th; Air Traj 7th; Scrambler 6th; Geo Maps 5th; Team 6th!
"Science Olympiad is, was, and always will be one of the greatest things that ever happened to me."
-
- Member
- Posts: 167
- Joined: December 28th, 2013, 10:59 pm
- Division: Grad
- State: CA
- Has thanked: 0
- Been thanked: 0
Re: Designs B/C
If your bridges always break along the compression between your braces your unbraced length is probably too high. I think going with option II would be more beneficial as the unbraced length is the same as option III but it also uses a little less wood. Also consider that the bracing in the axis perpendicular to this one may not be properly supported and could also be the cause of your troubles.Friedoyster3 wrote:A question about lateral bracing:
I've been constructing my lateral bracing on top of the compression member compression member like figure 1 below. However the last three bridges I've built have all failed along the compression member at the yellow circle. Which got me thinking, maybe I should try to do something like the second option to prevent a buckling failure of the compression member at near that type of node. What do you all think about this?
I've also been considering option III, which requires the lateral bracing to cross over one another with some really weird torques on the pieces. How should I go about constructing that? The one time that I tried option III, the two trusses separated without breaking because the lateral bracing connections at the nodes were too weak. Any ideas?
(This view is top down and does not represent the entire span, just a small section. Brown sticks are the compression members, red rectangles are truss nodes that extend into the screen, and blue sticks are lateral bracing.)
-
- Admin Emeritus
- Posts: 1115
- Joined: May 10th, 2011, 8:25 pm
- Division: Grad
- State: TX
- Has thanked: 0
- Been thanked: 1 time
Re: Designs B/C
How does it break? Does the compression assembly twist and snap at that point, or does that point just move sideways/up/down so far that it snaps? If the whole member twists, stick with option 1 and make the spacing a little closer, not half what you have now, but maybe 2/3 or 4/5. If it bends and snaps, option 2 would help, but make sure to support it from two perpendicular pieces (ie from the side and top, or side and bottom).
'If you're the smartest person in the room, you're in the wrong room' - Unknown
-
- Member
- Posts: 99
- Joined: February 1st, 2009, 6:38 am
- Division: C
- State: IN
- Has thanked: 0
- Been thanked: 0
Re: Designs B/C
The structure isn't so much twisting and breaking as it is deforming downwards. Across the entire span the deformation is actually quite noticeable. But since the break patterns aren't very conclusive, I can't really be 100% sure that's all that is happening to cause failure without high speed footage.iwonder wrote:How does it break? Does the compression assembly twist and snap at that point, or does that point just move sideways/up/down so far that it snaps? If the whole member twists, stick with option 1 and make the spacing a little closer, not half what you have now, but maybe 2/3 or 4/5. If it bends and snaps, option 2 would help, but make sure to support it from two perpendicular pieces (ie from the side and top, or side and bottom).
University of Michigan Aerospace Engineering
Munster High School, Indiana
2015 Nationals: Bridge 12th; Air Traj 7th; Scrambler 6th; Geo Maps 5th; Team 6th!
"Science Olympiad is, was, and always will be one of the greatest things that ever happened to me."
Munster High School, Indiana
2015 Nationals: Bridge 12th; Air Traj 7th; Scrambler 6th; Geo Maps 5th; Team 6th!
"Science Olympiad is, was, and always will be one of the greatest things that ever happened to me."
-
- Admin Emeritus
- Posts: 1115
- Joined: May 10th, 2011, 8:25 pm
- Division: Grad
- State: TX
- Has thanked: 0
- Been thanked: 1 time
Re: Designs B/C
Ahh the lengths I went to trying to get high speed footage of my structures breaking....Friedoyster3 wrote: The structure isn't so much twisting and breaking as it is deforming downwards. Across the entire span the deformation is actually quite noticeable. But since the break patterns aren't very conclusive, I can't really be 100% sure that's all that is happening to cause failure without high speed footage.
From how it sounds you could probably try horizontal braces, if the whole thing deforms try making it taller (I haven't read the rules enough to know if you can...?)
'If you're the smartest person in the room, you're in the wrong room' - Unknown
Who is online
Users browsing this forum: No registered users and 0 guests