What's your opinion on whether or not that vertical member should be there in the first place? I don't personally have enough experience to say. I know the guy who did Booms before me tried it both ways and settled on not, but I'd be curious to hear what more people think.SLM wrote:
1) If the boom is triangular but is missing the vertical member connecting the tension and compression members at the base, then the movement of the bolt in the hole could cause additional stress at the connection. If however, the vertical member is present, then the movement of the bolt most probably is not the cause of the failure. Regardless, you can always move the boom and the bolt downward as much as possible before tightening the nut. This way, the boom or the bolt has no more room to slide down once the structure is loaded.
There could be other reasons for the failure, but without being able to examine the boom closely it is difficult to say.
Boomilever for 2013
-
- Exalted Member
- Posts: 343
- Joined: November 14th, 2008, 5:17 am
- Division: Grad
- State: PA
- Has thanked: 0
- Been thanked: 0
Re: Boomilever for 2013
I'd also recommend just not using square tension members. Seems to me that would be the worst possible shape for them. Perhaps others disagree, though.
Harriton '10, UVA '14
Event Supervisor in MA (prev. VA and NorCal)
Event Supervisor in MA (prev. VA and NorCal)
-
- Member
- Posts: 195
- Joined: January 31st, 2009, 2:24 pm
- Division: Grad
- Has thanked: 0
- Been thanked: 0
Re: Boomilever for 2013
On the Bending of the Tension Member: When bending in a member is significant, as nejanimb mentioned, a square section is not the best option. Such a member carries a shear force and a bending moment. Both shear strength and bending strength are a function of the moment of inertia of the section. The larger the moment of inertia the stronger the member. For such a member, at the very least, a rectangular section should be used.
On Stress Concentration: It occurs whenever there is a change in the cross sectional area of the member. Stress concentration in a member increases when the cross-sectional area of the member decreases. For example, if a hole in punched in an otherwise solid rectangular member, stress around that hole increases since now stress has to flow through a smaller area. As Jeff mentioned, an abrupt change in the cross-section of the member results in a more crowded stress flow (higher stress) compared to the change in the stress flow caused by a smoother cross-sectional shape transition, as depicted below.

On the Need for a Vertical Member in the Triangular Boom: Here, I am referring to a vertical member that connects the tension member to the compression member at the wall. The member adds to the stability of the structure, it restricts relative movement of the ends of the boom at the wall. This may be particularly important for the compression member since its wall end is free to move up or down (although friction between the end of the compression member and the wall somewhat inhibits this movement). Regardless, I don’t see any disadvantage for having the member, except perhaps for the little weight that it adds to the structure. In my mind, its benefits (adding stability and certain level of performance consistency for the boom) outweighs its cost (the little added weight).
On Stress Concentration: It occurs whenever there is a change in the cross sectional area of the member. Stress concentration in a member increases when the cross-sectional area of the member decreases. For example, if a hole in punched in an otherwise solid rectangular member, stress around that hole increases since now stress has to flow through a smaller area. As Jeff mentioned, an abrupt change in the cross-section of the member results in a more crowded stress flow (higher stress) compared to the change in the stress flow caused by a smoother cross-sectional shape transition, as depicted below.

On the Need for a Vertical Member in the Triangular Boom: Here, I am referring to a vertical member that connects the tension member to the compression member at the wall. The member adds to the stability of the structure, it restricts relative movement of the ends of the boom at the wall. This may be particularly important for the compression member since its wall end is free to move up or down (although friction between the end of the compression member and the wall somewhat inhibits this movement). Regardless, I don’t see any disadvantage for having the member, except perhaps for the little weight that it adds to the structure. In my mind, its benefits (adding stability and certain level of performance consistency for the boom) outweighs its cost (the little added weight).
-
- Member
- Posts: 30
- Joined: September 16th, 2011, 6:05 pm
- Division: C
- State: MI
- Has thanked: 0
- Been thanked: 0
Re: Boomilever for 2013
Suppose a boomilever base was a solid, square piece of wood with a hole drilled in the middle and the tension members glued to the outside at the 3 o'clock and 9 o'clock positions. Would it be better for the wood grain of the base to run vertically or horizontally?
Last edited by Faustina on July 10th, 2012, 11:55 am, edited 1 time in total.
-
- Admin Emeritus
- Posts: 1115
- Joined: May 10th, 2011, 8:25 pm
- Division: Grad
- State: TX
- Has thanked: 0
- Been thanked: 1 time
Re: Boomilever for 2013
Ideally the grain would run through the tension members and the hole. Think about bending a balsa sheet, if you bend it into a tube with the grain running the length of the tube, it's not to hard to bend, however if you try and bend it the other way, it's significantly harder, and since the tension members and the bolt are in essence trying to bend the base, they should be trying to bend the wood along the grain(the stronger way), not perpendicular to it(the weaker way).
'If you're the smartest person in the room, you're in the wrong room' - Unknown
-
- Member
- Posts: 195
- Joined: January 31st, 2009, 2:24 pm
- Division: Grad
- Has thanked: 0
- Been thanked: 0
Re: Boomilever for 2013
I agree with iwonder. Although there are multiple forces acting on the base plate, the most prominent ones are the forces that tend to bend the plate outward (away from the support). Therefore, for analysis purposes, it is best to view the base plate as a beam. As such, wood fibers need to run horizontally along the length of the beam, between 3 o'clock and 9 o'clock positions.Faustina wrote:Suppose a boomilever base was a solid, square piece of wood with a hole drilled in the middle and the tension members glued to the outside at the 3 o'clock and 9 o'clock positions. Would it be better for the wood grain of the base to run vertically or horizontally?
-
- Member
- Posts: 1649
- Joined: April 30th, 2007, 7:54 am
- Has thanked: 0
- Been thanked: 29 times
Re: Boomilever for 2013
While the explanation is a little simple, the conclusion and drawing are correct. Sharp changes in cross section cause stress concentrations that lead to premature failure. Avoid them.SLM wrote:[<SNIP>On Stress Concentration: It occurs whenever there is a change in the cross sectional area of the member. Stress concentration in a member increases when the cross-sectional area of the member decreases. For example, if a hole in punched in an otherwise solid rectangular member, stress around that hole increases since now stress has to flow through a smaller area. As Jeff mentioned, an abrupt change in the cross-section of the member results in a more crowded stress flow (higher stress) compared to the change in the stress flow caused by a smoother cross-sectional shape transition, as depicted below. <SNIP>
Seperately, test surface. Be aware, many tournament test surfaces are smooth, slippery melamine that provides almost NO resistance to unrestrained parts from moving out of alignment. Thus my recommendation to stabilize the lower compression members with some sort of connection to the base. IF everything stays perpendicular there is no tendency to move. BUT, its rare that everything is perfect and there is some small force to move that gets larger as it goes unless restrained initially.
Jeff Anderson
Livonia, MI
-
- Member
- Posts: 81
- Joined: May 14th, 2001, 6:54 pm
- Division: Grad
- State: IN
- Has thanked: 0
- Been thanked: 0
Re: Boomilever for 2013
I think this depends on how tall the compression piece is. When this was an event for the first time back in 2001, we tested several ideas for compression pieces that ranged from 5 cm tall pieces (built as a tower on its side) all the way down to something close to 1 cm tall ones. We've tried smaller heights since then. In general, we've found that the need for vertical bracing between the tension and compression members increases as the height of the compression member decreases. Also, as the height of the compression member continues to get smaller from the point at which one vertical on each side is needed, at some point you find that you do better with multiple vertical members on each side. Case in point is that the shortest compression piece I've ever seen built into a boom used two 3/16" square bass pieces for the compression member, one on each side, so the compression member height was 3/16". That one used several vertical members on each side (on the order of 6), and went very close to 15 kg if not all the way. The most memorable part, however, was how much those two sticks contorted and bent in multiple directions without breaking as it was loaded. I was very surprised that went as far as it did. We decided to not compete with that design, due to not trusting any two booms to be even remotely close to the same. Anyway, at some point we landed on a compression member whose height calls for one vertical brace on each side, so it was much stiffer against bending. We did a very respectable 7th at nats in 2007 and 5th in 2008 in the event.What's your opinion on whether or not that vertical member should be there in the first place? I don't personally have enough experience to say. I know the guy who did Booms before me tried it both ways and settled on not, but I'd be curious to hear what more people think.
-
- Admin Emeritus
- Posts: 1115
- Joined: May 10th, 2011, 8:25 pm
- Division: Grad
- State: TX
- Has thanked: 0
- Been thanked: 1 time
Re: Boomilever for 2013
I was planning to have my compression member indpendent from the tension memebers, so the compression member doesn't buckle in any direction without bracing from the tension members, however I was going to put ultralight connections at the testing wall to maintain proper spacing, they wouldn't be strong enough to correct the error if the base were to slide down during loading, as was experienced before... Does this seem reasonable? Any thoughts? I'm about to buy some wood and start building one for test so I'm looking to firm up on a basic design(for the one I'm building, not the season
) before I go order anything from specialized.
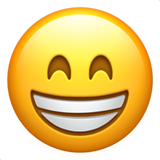
-
- Member
- Posts: 30
- Joined: September 16th, 2011, 6:05 pm
- Division: C
- State: MI
- Has thanked: 0
- Been thanked: 0
Re: Boomilever for 2013
I would say that it seems reasonable, as long as your compression is tall enough (see JimY's post). Having at least one vertical piece per side probably makes it easier to set up the boomilever on the wall.iwonder wrote:I was planning to have my compression member indpendent from the tension memebers, so the compression member doesn't buckle in any direction without bracing from the tension members, however I was going to put ultralight connections at the testing wall to maintain proper spacing, they wouldn't be strong enough to correct the error if the base were to slide down during loading, as was experienced before... Does this seem reasonable? Any thoughts? I'm about to buy some wood and start building one for test so I'm looking to firm up on a basic design(for the one I'm building, not the season) before I go order anything from specialized.
Also, I made two changes to my boomilever: smaller hole on the base, larger and rectangular cross-section of tension members. This doubled the amount of weight the boom held. Thanks everybody for helping me out. The efficiency wasn't that great (~900), but I've learned a ton.
- fishman100
- Exalted Member
- Posts: 478
- Joined: January 28th, 2011, 1:26 pm
- Division: Grad
- State: VA
- Has thanked: 0
- Been thanked: 0
Re: Boomilever for 2013
The draft rules are being presented tonight!
On another note, would testing the tension and compression members separately (think Towers; testing the base and the chimney separately to see if each could hold the required amount of weight) be a good idea? If so, any ideas on how would one do that since the load on the compression structure? Flipping the structure 90 degrees so it's upright (like a chimney of a tower) and then applying the load from the top down won't work, since on a boom the load isn't equally distributed.
On another note, would testing the tension and compression members separately (think Towers; testing the base and the chimney separately to see if each could hold the required amount of weight) be a good idea? If so, any ideas on how would one do that since the load on the compression structure? Flipping the structure 90 degrees so it's upright (like a chimney of a tower) and then applying the load from the top down won't work, since on a boom the load isn't equally distributed.
Langley HS Science Olympiad '15
Who is online
Users browsing this forum: No registered users and 0 guests